Understanding the Importance of the Best Rotary Blowout Preventer: A Comprehensive Guide
2025-03-28
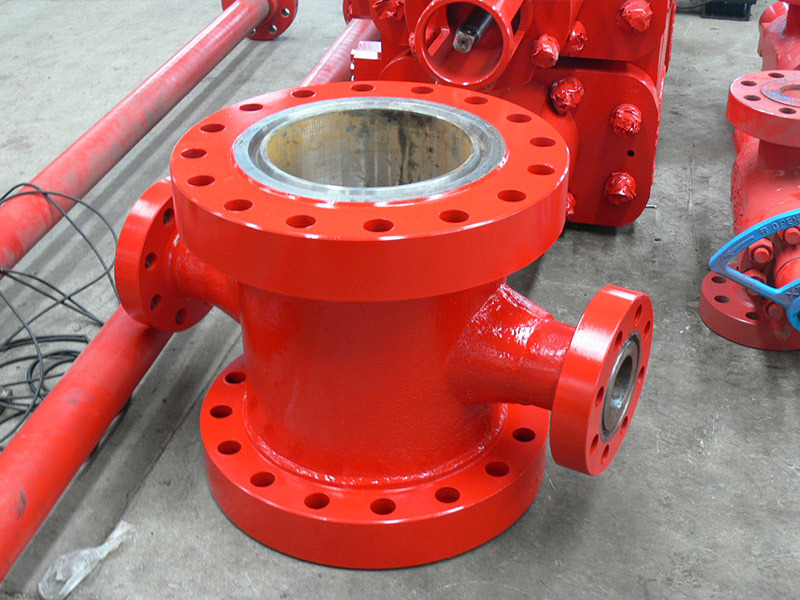
Understanding the Importance of the Best Rotary Blowout Preventer
Table of Contents
- 1. Introduction to Rotary Blowout Preventers
- 2. What is a Rotary Blowout Preventer?
- 3. Types of Blowout Preventers: A Detailed Overview
- 4. Key Features of a High-Quality Rotary Blowout Preventer
- 5. The Importance of Rotary Blowout Preventers in Drilling Operations
- 6. Best Practices for Choosing the Right Rotary Blowout Preventer
- 7. Maintenance and Inspection of Rotary Blowout Preventers
- 8. Conclusion
1. Introduction to Rotary Blowout Preventers
In the oil and gas industry, controlling the pressure during drilling operations is crucial to prevent catastrophic blowouts. This is where the importance of a **Rotary Blowout Preventer (BOP)** comes into play. As a vital safety mechanism, the BOP serves as a barrier against the uncontrolled release of oil, gas, or water from a well. Understanding how Rotary Blowout Preventers function and their critical role in maintaining safety standards is essential for any drilling operation.
2. What is a Rotary Blowout Preventer?
A **Rotary Blowout Preventer** is a type of blowout preventer specifically designed to seal a well in case of a sudden pressure surge. It functions by creating a barrier around the drill pipe, effectively preventing fluids from escaping. Typically employed in offshore drilling operations, the rotary BOP is essential for managing high-pressure situations and ensuring the safe extraction of resources.
2.1 How Does It Work?
When pressure surges occur, the rotary BOP activates its closing mechanism, which can involve hydraulics or mechanical systems. This swift response is crucial in averting potential disasters. The BOP's ability to adapt to varying conditions while maintaining a seal is what sets it apart from other blowout preventers.
3. Types of Blowout Preventers: A Detailed Overview
Understanding the different types of blowout preventers is vital for selecting the most suitable one for your operations. The two primary types are:
3.1 Annular Blowout Preventers
Annular BOPs create a seal around the entire circumference of the drill pipe. They are versatile and can accommodate various pipe sizes, making them ideal for different drilling scenarios.
3.2 Ram Blowout Preventers
Ram BOPs utilize metal rams to seal off sections of the well. They are categorized into two main types: pipe rams and blind rams, each serving distinct functions during drilling operations.
4. Key Features of a High-Quality Rotary Blowout Preventer
When selecting a rotary blowout preventer, several features should be considered to ensure its effectiveness and reliability:
4.1 Durability
The materials used in constructing the BOP should withstand extreme pressures and harsh environmental conditions, ensuring a long lifespan.
4.2 Response Time
A high-quality rotary BOP should activate within seconds of detecting pressure surges. Fast response times are critical for preventing blowouts.
4.3 Maintenance Accessibility
Ease of maintenance is crucial. A BOP that is designed for straightforward inspection and servicing can significantly reduce downtime during operations.
4.4 Compatibility
Selecting a BOP that is compatible with existing drilling equipment ensures smooth integration and operation.
5. The Importance of Rotary Blowout Preventers in Drilling Operations
Rotary blowout preventers play a critical role in ensuring safety during drilling operations. Their importance can be highlighted through several key aspects:
5.1 Risk Mitigation
The primary function of rotary BOPs is to mitigate risks associated with high-pressure scenarios. By providing a reliable seal, they greatly reduce the likelihood of blowouts, which can result in substantial financial losses and environmental disasters.
5.2 Regulatory Compliance
Many regions have strict regulations governing drilling operations. Implementing rotary blowout preventers is often mandated to comply with safety standards, thus avoiding legal repercussions.
5.3 Enhancing Operational Efficiency
Incorporating rotary BOPs into drilling operations can enhance efficiency. By preventing blowouts, they reduce the need for costly clean-up operations and allow projects to stay on schedule.
6. Best Practices for Choosing the Right Rotary Blowout Preventer
Selecting the appropriate rotary blowout preventer involves careful consideration of various factors to ensure maximum safety and efficiency:
6.1 Assessing Operational Requirements
Evaluate the specific requirements of your drilling operations, including the expected pressure, fluid type, and environmental conditions. This assessment will guide your selection.
6.2 Consulting with Experts
Engaging with experts in the field can provide valuable insights into the best rotary blowout preventers available. Their experience can help you avoid potential pitfalls and make informed decisions.
6.3 Investing in Quality
Opting for high-quality, certified rotary BOPs is crucial. While they may have a higher upfront cost, their reliability and durability can lead to significant savings in the long run.
7. Maintenance and Inspection of Rotary Blowout Preventers
Regular maintenance and inspection of rotary blowout preventers are vital to ensure their continued effectiveness:
7.1 Scheduled Inspections
Implementing a regular inspection schedule can help identify potential issues before they escalate, ensuring the BOP functions optimally when needed.
7.2 Documenting Maintenance Activities
Keeping detailed records of maintenance activities aids in tracking the performance of the BOP over time, providing insights into any necessary adjustments or replacements.
7.3 Training Personnel
Training personnel on proper maintenance procedures and emergency protocols ensures that everyone involved is prepared to respond promptly in case of a pressure surge.
8. Conclusion
In conclusion, the significance of rotary blowout preventers in the oil and gas industry cannot be overstated. By understanding their functionality, types, and the critical role they play in maintaining safety during drilling operations, companies can make informed decisions that protect their investments and the environment. Choosing the right rotary blowout preventer, coupled with regular maintenance and expert guidance, ensures that drilling operations remain safe, efficient, and compliant with regulations. Investing in a high-quality rotary BOP is not just a regulatory requirement; it is a commitment to safety and operational excellence in an often unpredictable industry.
FAQs
1. What is the primary function of a rotary blowout preventer?
The primary function of a rotary blowout preventer is to seal a well and prevent uncontrolled releases of oil, gas, or water during drilling operations.
2. How do I choose the right rotary blowout preventer for my operation?
Choosing the right rotary blowout preventer involves assessing your operational requirements, consulting with industry experts, and investing in high-quality equipment.
3. What are the maintenance requirements for a rotary blowout preventer?
Regular inspections, scheduled maintenance, and training personnel on proper maintenance procedures are essential for ensuring the effectiveness of a rotary blowout preventer.
4. What are the risks of not using a rotary blowout preventer in drilling operations?
Not using a rotary blowout preventer can lead to catastrophic blowouts, resulting in significant financial losses, legal repercussions, and environmental damage.
5. Are rotary blowout preventers used only in offshore drilling?
While rotary blowout preventers are commonly used in offshore drilling, they are also applicable in onshore operations where high-pressure situations exist.
Related News
Contact Us
Mailbox:
tiehu@tiehupetro.com
Telephone:
86-317-2616808
Address:
Yanling Industrial Zone, Renqiu City, Cangzhou City, Hebei Province, China